Fall 2023 Newsletter
Summer Field Work: Sierra Leone & Mozambique
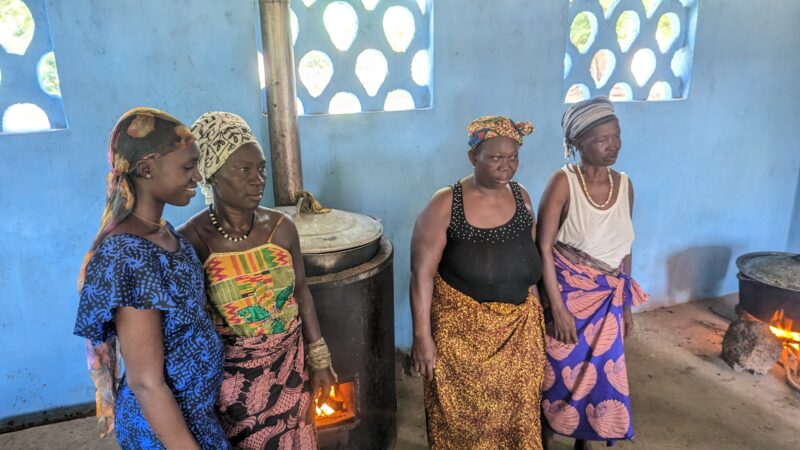
Field work is one of the most important aspects of our theory of change here at BDL. This summer, BDL engineers put that theory into action, travelling to project sites in Sierra Leone and Mozambique.
Typically, we begin our new cookstove projects by identifying a country’s traditional stove uses and performances. We then learn about their cultural cooking traditions and review any improved stove models in use. If there are existing stove manufacturing operations, we visit them and identify potential supply chains for improved stove materials and tools. Finally, we examine opportunities and challenges for new manufacturing (and stove sales) projects. All of this work can be achieved only by spending significant time on the ground.
Sierra Leone is the site of our institutional stove project with our partner Westwind Energy (WWE) where we’re working to address a serious issue: the practice of preparing school meals on open fires that require enormous amounts of biomass fuel and that put cooks’ health at risk from smoke exposure and burn danger.
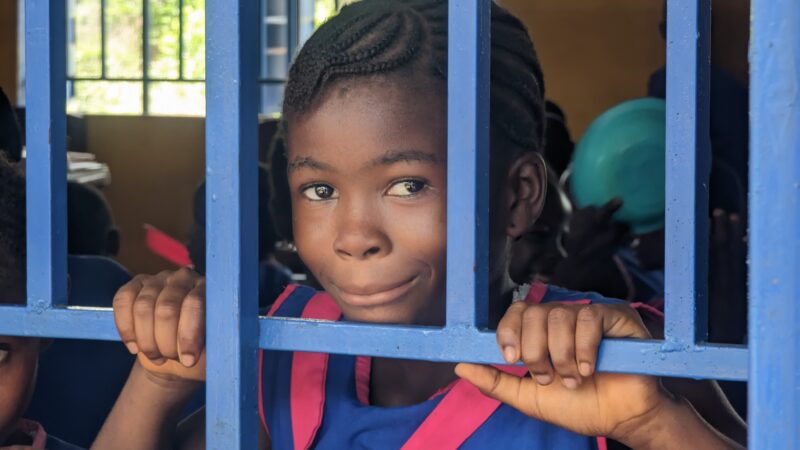
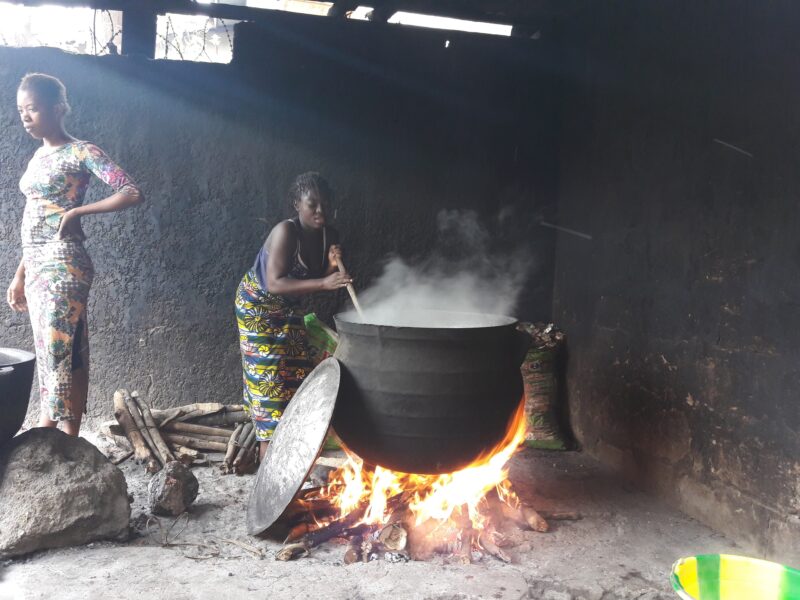
A 2022 survey by the U.N.’s World Food Programme found that the typical Sierra Leonean school used on average 60 kilograms of firewood per day cooking meals on the traditional three stone fire (60 kilograms is 132 pounds). It also found that the three stone fires took more than seven times the amount of fuel than a locally made improved stove and that it took longer to cook food on these fires than on improved stoves. Improved stoves are also cleaner, ensuring that school children will eat their meals in kitchens that are cleaner and where they are less likely to be exposed to harmful smoke and air pollution.
WWE, a local manufacturer in Sierra Leone, developed an institutional stove that begins to address these issues. At WWE’s request, BDL is now working with WWE to improve its institutional cookstove by enhancing both its efficiency and durability and reducing its cost. BDL is also partnering with WWE to develop a manufacturing system capable of producing 300 stoves per month, up from the current 20 stoves per month.
During their trip to Sierra Leone this summer, our team members Aaron Nyarkotey, Gary Robertson, and Justin Wimpey visited Westwind Energy’s facility, where they assessed the components that go into building WWE’s institutional stove, as well as staff capacity and the equipment the factory has in place. This kind of assessment is critical: It enables our project engineers to develop a computer model of the current design, which in turn allows us to identify more efficient and cost-effective manufacturing processes and design an upgraded manufacturing system.
The visit to Sierra Leone also enabled us to strengthen partnerships and collaborations with other organizations working to develop cleaner cooking situations in the country, including the Ministry of Education. The Ministry is supportive of BDL and Westwind Energy’s collaboration to make school cooking healthier, easier, and better for the environment.
This project represents an important opportunity for both BDL and for you, our supporters. While other projects focus on improving the health of home cooks, the Sierra Leone project takes the role of clean stove technology even farther: It helps to improve educational opportunities for children, particularly girls. Students who can access school lunches are more likely to attend school and stay in school. Students also begin to see the tangible benefits of clean energy, often bringing that knowledge to their homes, where they help their families understand the importance of adopting healthier and more efficient cooking practices.
A different story is playing out in Mozambique, on the other side of the continent, the site of our newest improved cookstove project. Two of our engineers – Charlie Sellers and Cooper Sloan just returned from a visit there. Over the last 10 years, Mozambique’s fastest growing cities have seen such a growth in the consumption of charcoal for cooking that charcoal prices have increased by more than 200%. There are not enough forests left in the country to meet the demand for charcoal production. The only answer to this dire situation is to help Mozambique find more efficient cooking methods – methods that use far less fuel.
That’s where BDL comes in. We’re working with the United Nations Development Program (UNDP) to design an improved stove that is more durable, is more efficient, has lower emissions, costs less, and, of course, meets the cultural and functional needs of the people who use them. The development of this new stove design and implementation begins with the user and their cooking culture. We have already started with a proven design, which we’ll modify and improve based on user feedback. Finally, we plan to work with local manufacturers and supply chain entities so as to enable the stoves to be produced in-country.
This scoping visit taught our engineers a few things about the cooking landscape in Mozambique. The market for improved stoves is in a very early stage: There’s little community awareness about the importance of improved cooking and minimal technological capability. Charlie noted that he has never seen so few improved stoves – either locally made or imported – available to a community. While this represents a major challenge for BDL and the UNDP, it is also a perfect example of why we do this work and take on difficult projects. Simply put, the need is great.
We're an ASME ISHOW-USA 2023 WINNER!
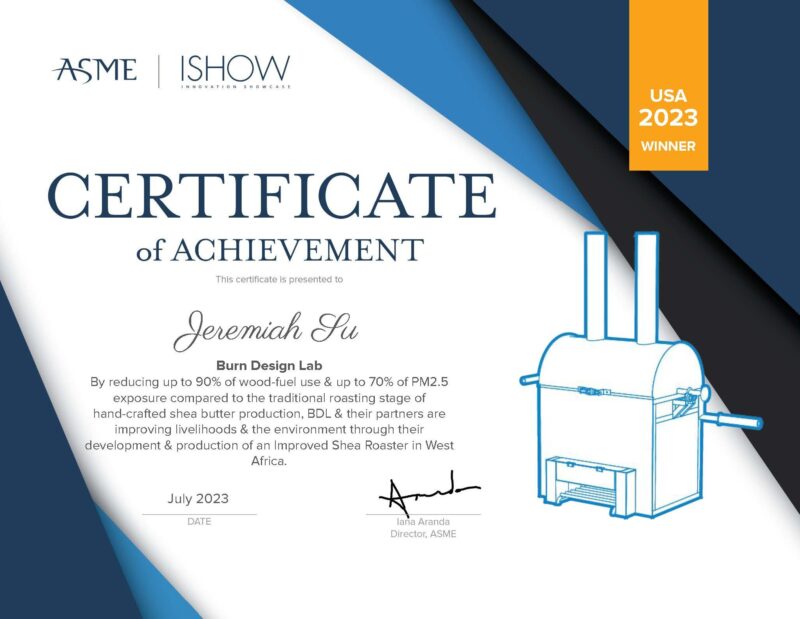
The American Society of Mechanical Engineers (ASME) announced in July the regional winners of the 2023 ASME Innovation Showcase (ISHOW), the prestigious international accelerator of hardware-led social innovation. Eight social ventures from throughout the Americas and England presented design prototypes at ASME ISHOW USA held virtually July 18-26. Three of these ventures, including Burn Design Lab, emerged as regional ISHOW USA winners. We will share in seed grants and receive technical support to help bring our design innovation to market.
BDL won for our Improved Shea Nut Roaster – an improved shea roaster that reduces up to 90% of wood-fuel use and up to 70% of PM2.5 exposure compared to the traditional roasting stage of hand-crafted shea butter production, improving livelihoods and the environment in West Africa.
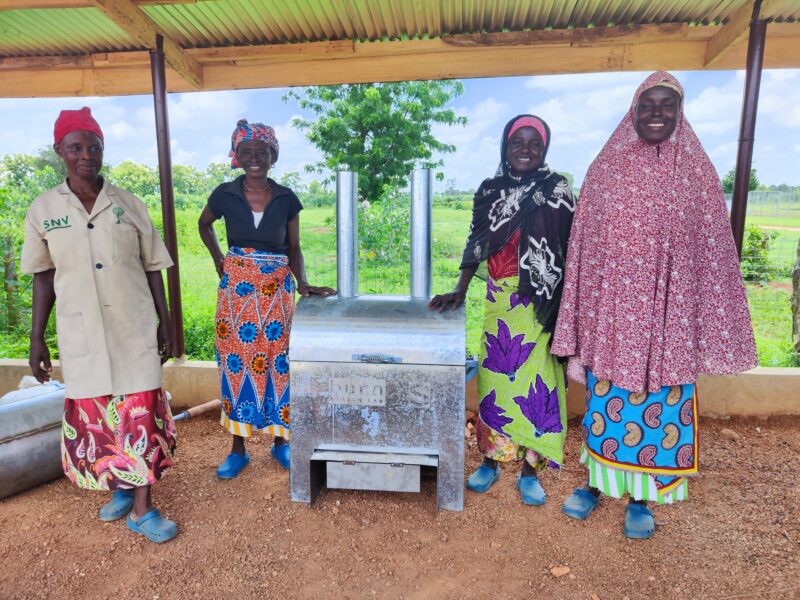
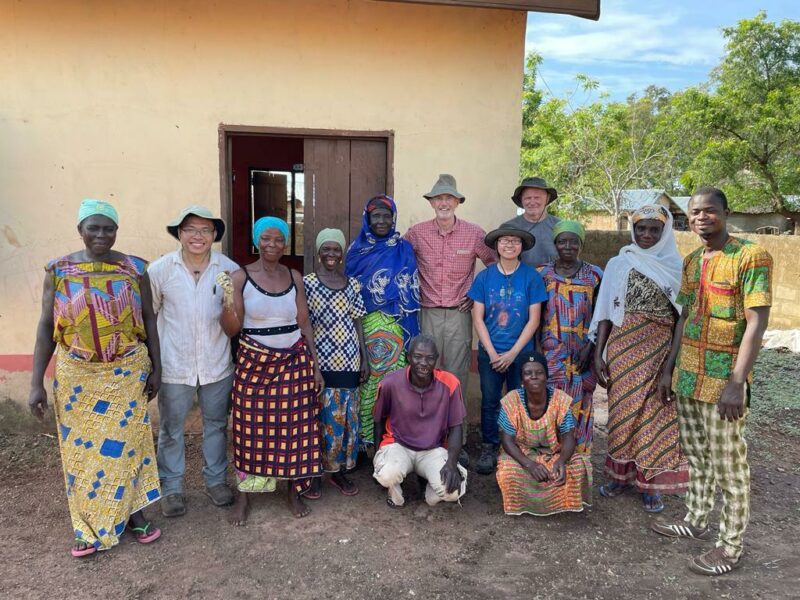
“We are proud to offer a forum for engineering problem-solving that truly improves lives,” ASME Executive Director/ CEO Tom Costabile said. “We are continually impressed by the creative talent of ASME ISHOW participants, their focus on sustainable solutions, and their passion for helping underserved communities around the world."