Summer 2021 Newsletter
Ghana Blog Excerpt
In June, 2021, the Improved Shea Roaster Project Team traveled to Ghana to conduct field tests, meet with potential manufacturers, and gather feedback from the women. Here is an excerpt from:
Photos and Words from Ghana
By Jeremy Su, Improved Shea Roaster Project Manager
This trip, project, and the product I have been working on are a couple years in the making. Before me, there were others who documented their work through photos, videos, reports, and designs. I knew the general project goals, and I knew the conditions, issues, and problems that the women face. But I didn’t see it with my own eyes, hear it from the women sitting in front of me, breath the same smoke they breath in every day, rotate the same drum for hours a day, feel the same heat of the fire, and go to bed with the same stinging in my eyes every night.
I came to BDL to be closer to the problem, so that I could better understand the issues people face, in order to make a larger impact through my work. I told Paul this coming in, and that I was a firm believer that there is only so much work that we, as an organization, can do here on an island in the Puget Sound before it is necessary for us to visit the local communities. Understanding that we were in the midst of a global pandemic, patience was necessary. When the trip did come around, I almost didn’t believe it until our plane took off from Seattle.
The trip went by so fast, and we had amazing results from the prototype. More importantly, I am grateful for the opportunity to share the time with the women who process shea butter every day. I am grateful to have learned from them and with them throughout the trip. I am grateful that our prototype was received with dancing and singing. I am grateful for the chance to see it with my own eyes, hear the feedback from the women sitting in front of me, and experience the same smoke, heat, and pain from processing shea butter over those four days. Because without their input and feedback, and our shared experience and understanding during trips, such as this one, we would not be able to improve lives and the environment in these communities full of amazing people.
To read the rest of the Jeremy’s and the team’s account of the latest trip to Ghana, please visit: www.burndesignlab.org/blogs
Volunteer Spotlight
Lou Fezio is one of our dedicated volunteers. Lou spent most of his career working for K2, a ski and snowboarding company. His exciting work there included crucial technology like triaxial braiding and a lightweight, low-cost board molding system which K2 still uses today. In 2011, Lou began volunteering for Burn Manufacturing (BMC) in his free time while still at K2. Eventually, after 30 years of working at K2, Lou decided to retire and fully dedicate his time to BMC.
Lou worked with BMC from 2011 to 2019 and continued to demonstrate his excellence within the engineering field. He worked in product design and managed BMC’s factory construction, where he planned the layout and improved equipment and tooling. Once Lou retired (for the second time), Paul Means, BDL Executive Director, reached out to see if he would be interested in volunteering for BDL. Lou shared that the reason he started volunteering with BDL was that he “had the free time, so why not help out a great cause.”
Recently, Lou has been a strong resource on our factory improvement project in Lira, Uganda. He has been utilizing his experience from K2 and BMC to modify tooling which will assist in the factory’s stove production. He’s also been a great mentor for all our young engineering staff and interns, bringing breadth of experience and knowledge to the table. When Lou’s not volunteering for BDL, he’s fixing bikes and other tools and appliances at the local thrift store, Granny’s Attic, which the BDL team loves to visit!
We cannot thank Lou enough for all the help and support he has given to BDL and continues to give!
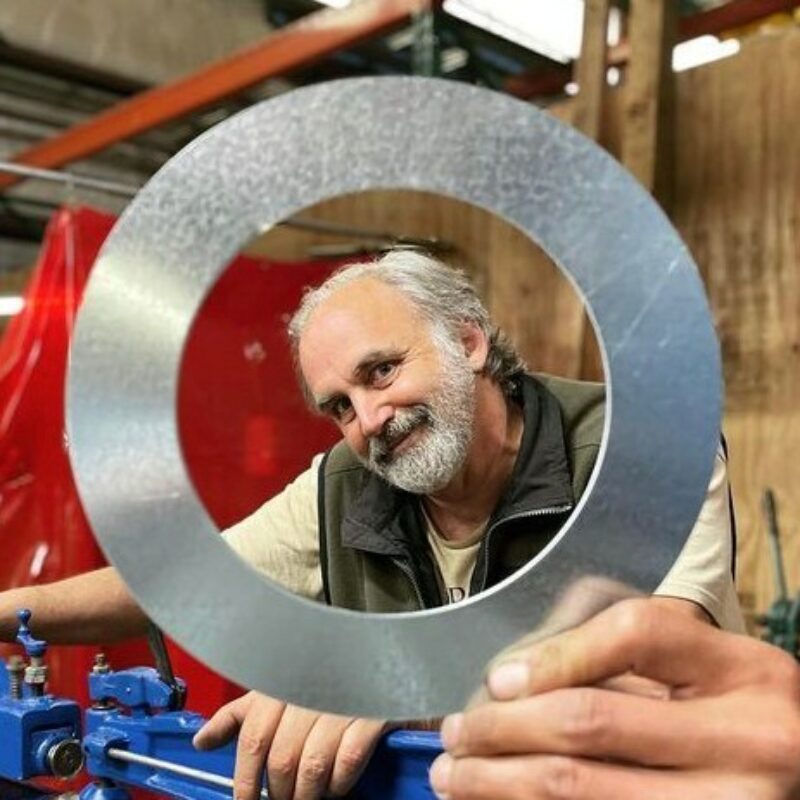
Lira Project Update
With the COVID situation in Uganda improving, BDL Engineer Emilio Taltique and Volunteer Charlie Sellers left for six week long trip at the beginning of August. The trip had several objectives, the first of which was to obtain quotes on different infrastructure improvements. They also are working on implementing Lean Manufacturing Principles of "5S" to better utilize the space already available. Another task was to "ground truth" the current BDL drawings and process flow map by closely monitoring the manufacturing process and measuring the parts being produced. The team is gaining feedback on several of the tools developed such as hand folders and an improved arbor for the bicycle grinding wheel.
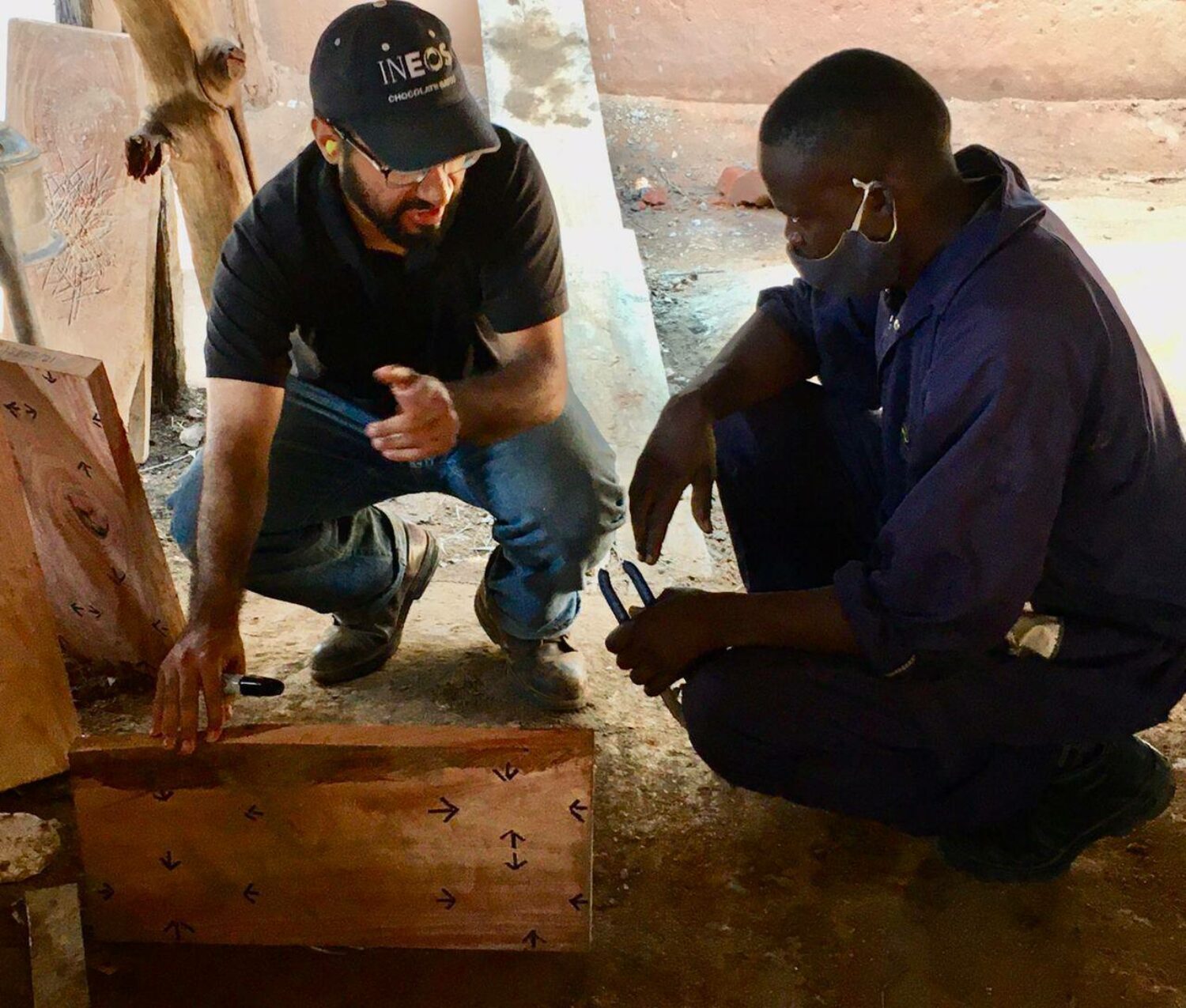
Emilio implementing a wood block to prevent the practice of chiseling in the dirt. This keeps parts clean and prevents chisels from wearing too soon. After new equipment is brought in, chiseling will no longer be necessary.
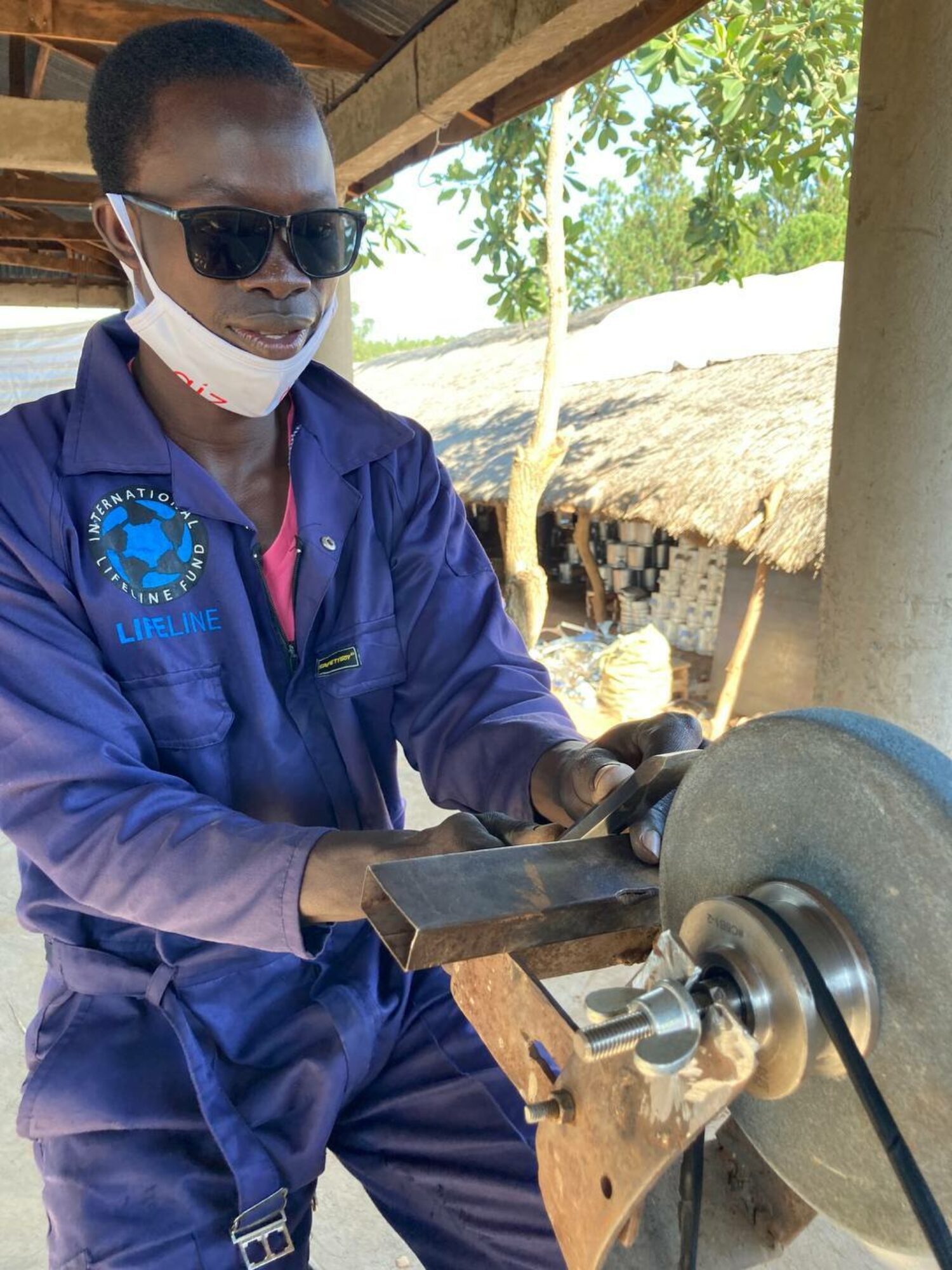
Simon, a fabricator at the factory, is using the improved arbor for the bicycle grinding wheel. The arbor was designed by Bryan Willman to be easier to change wheels when they wear down and has less wobble than the previous design
Back at BDL, the travel team is supported by BDL engineer Louisa Anderson and longtime volunteers Bryan Willman and Lou Fezio. The team is currently working on making adaptations to different machines, so they are more appropriate for their future setting in Lira. By calculating different process timings, they can determine how many machines are needed to meet the factory's production goal of 15,000 stoves per month. Elise Clement and Andrew Killian were also on the Lira project and just wrapped up their internships. Elise worked on nesting diagrams for cutting parts out of the sheet metal as well as making adaptations to the shears that will be sent to Lira. Andrew was able to help with testing bending and flanging equipment to determine if they will help the factory meet its new production goals. BDL is grateful for their time here and wishes them well as they head back to the University of Dayton!
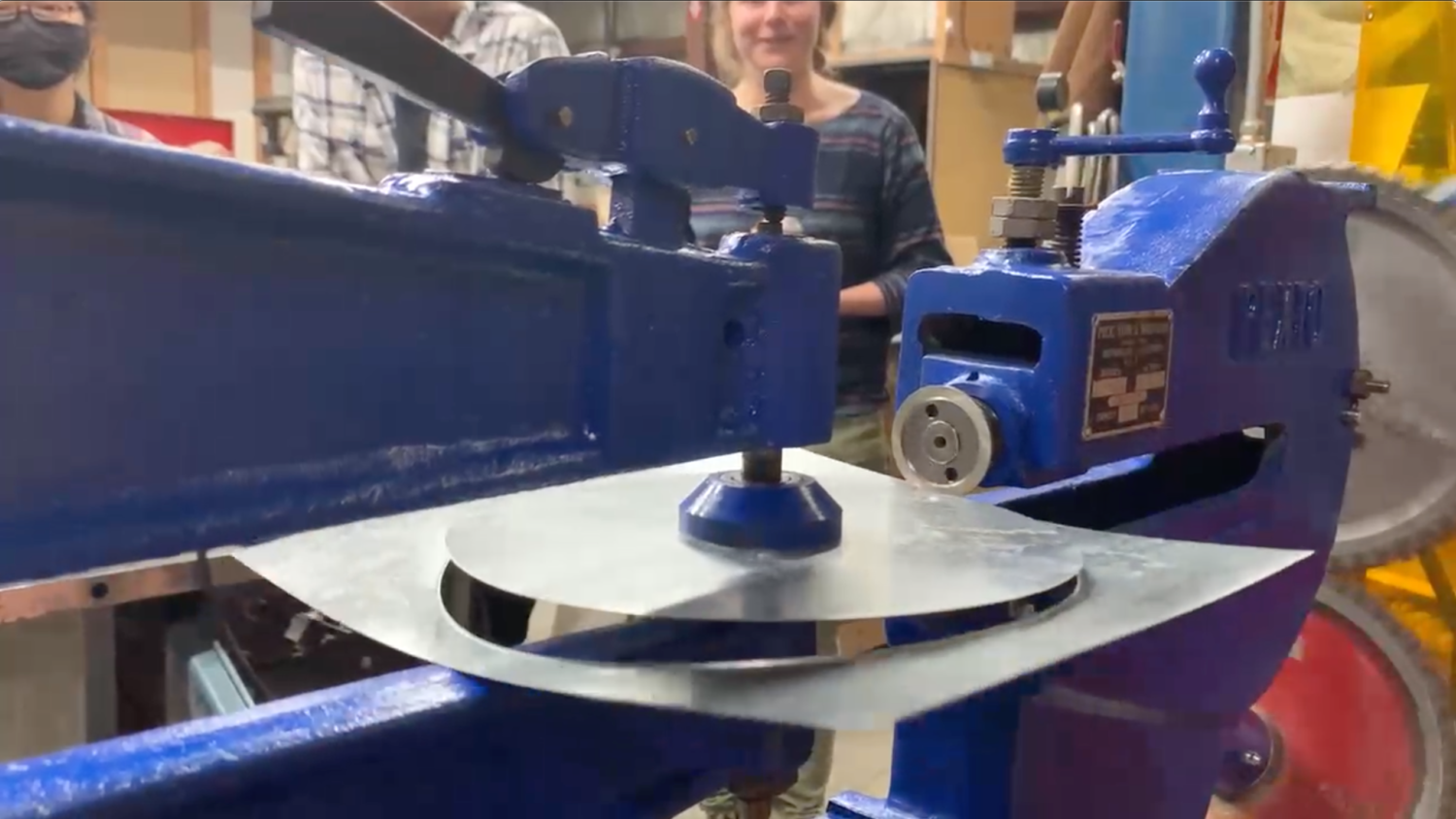
Lou Fezio demonstrating the use of the refurbished circle shear to make stove bottoms and rings more efficiently and consistently.
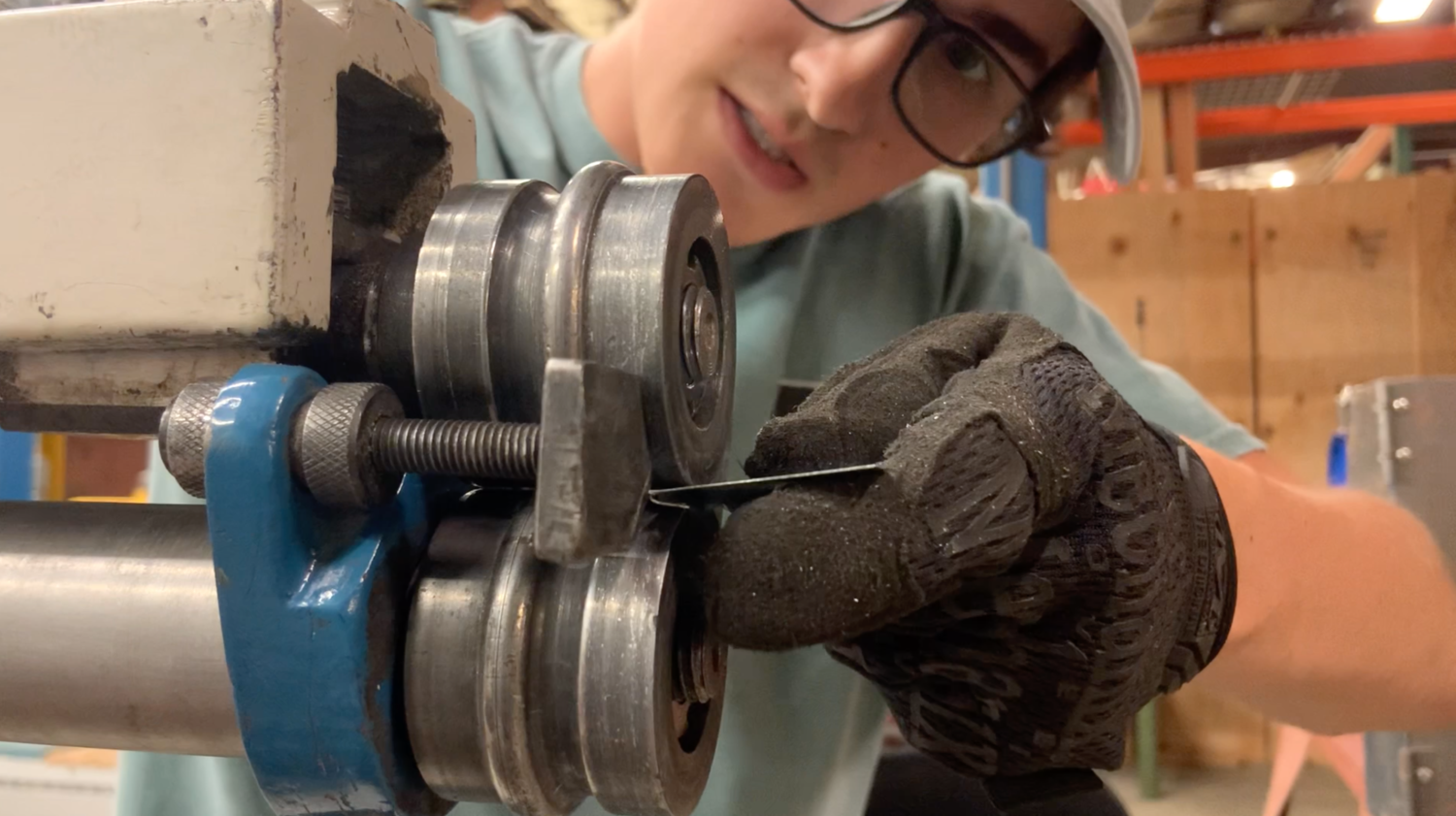
Summer intern, Andrew Killian, working on closing hems with a bead roller to help improve the process in the ILF Factory in Uganda.
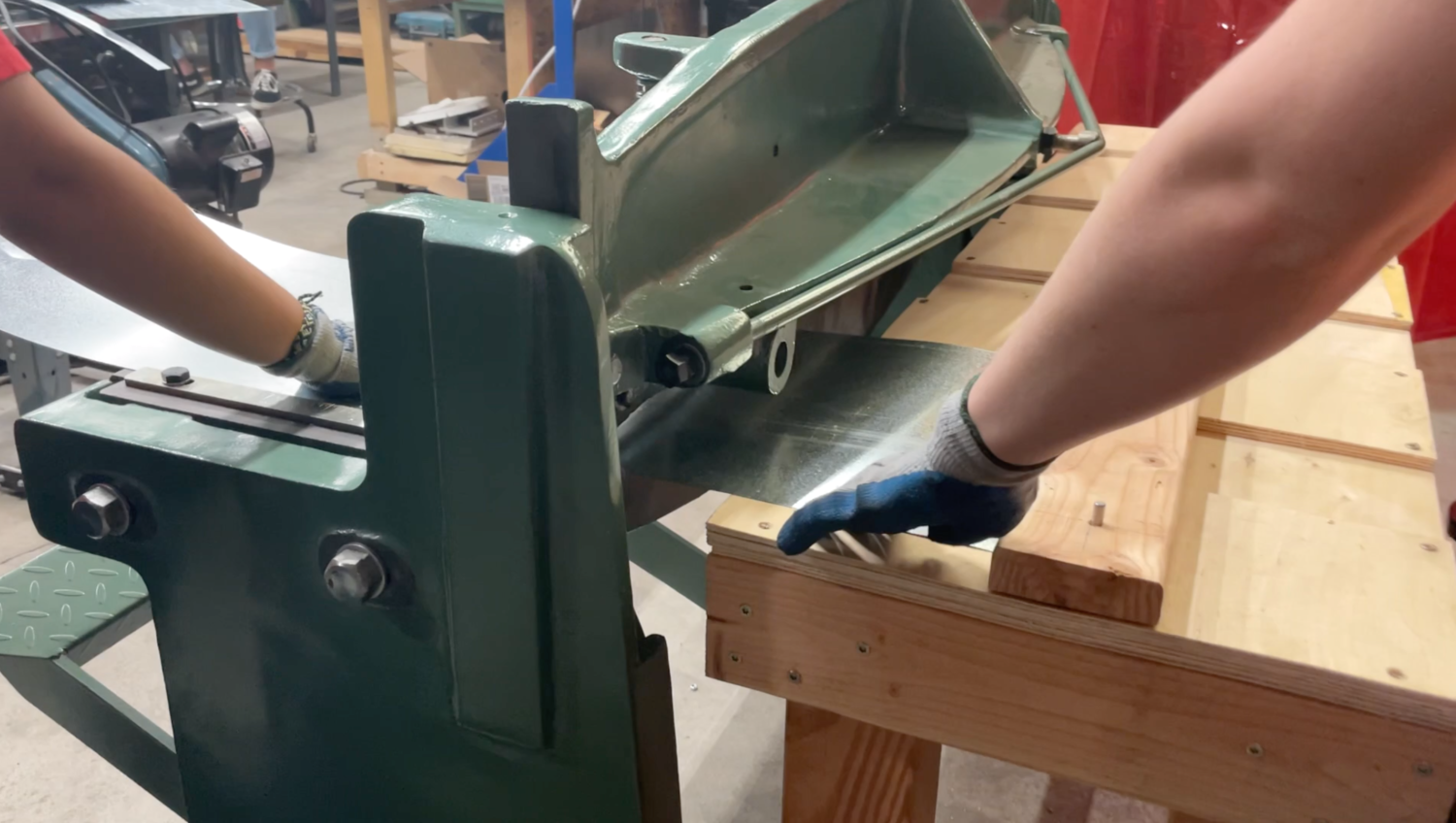
Summer intern, Elise Clement, demonstrating the use of the table shear stop system she worked on during her summer internship at BDL.
With all of these changes coming the team is maintaining the human centered design approach by making the factory workers a part of the decision making process and responding to their feedback. The current trip has helped the project gain some steam because the presence of the BDL team has removed roadblocks for several projects and gained access to more information not uncovered on the first trip. The visit has also been important to the team because the full impact of the project was somewhat lost when just reviewing photos and reports of the factory. But meeting the people at the factory who are hoping for change has given the project a whole new sense of meaning.
Going forward, the team plans on assisting with training the new Head of Operations at the factory, overseeing construction of new workspaces, and bringing in the new tools and equipment that the team on Vashon has been modifying and testing!
Please consider donating to our ILF Factory Improvement Project to allow us to continue making improvements to their factory with the goal of increasing production to 15,000 stoves per month!
Shea Project Update
Paul Means, Executive Director, Jeremy Su, Shea Project Manager, and Brandy Tang, Lab Manager visited Ghana in June of 2021 to test the latest prototype, vet an initial selection of manufacturers, as well as meet with potential partners and interested parties around Ghana. To hear more about the trip, please view everyone’s account at our blog, or view our Q3-2021 update of the project in the video below:
BDL Improved Shea Roaster - Q3 Update
After returning from the Ghana trip in June, the Improved Shea Roaster Project team is working to increasing the efficiency to at least 40%, work with more Ghanaian manufacturers, and continue work on our Ergonomic Drive Mechanism and Alternative Fuels. Lead engineer, Jeremy Su, is spearheading the project and designing the more efficient roaster while communicating with the manufacturers and partners in Ghana. He was joined by summer intern, Cooper Sloan, to develop the Ergonomic Drive Mechanism this past summer and his work is continued by current Northeastern co-op student, Thando Ray. Thando will also be diving into a study of shea cake, the biomass byproduct of the shea butter process, as an alternative fuel here in our lab. All this is being done in preparation for a follow up trip in November as well as the initiation of the Pilot Phase of the project early next year.
Summer intern, Cooper Sloan, demonstrating the ergonomic drive mechanism he developed over the course of his summer internship.
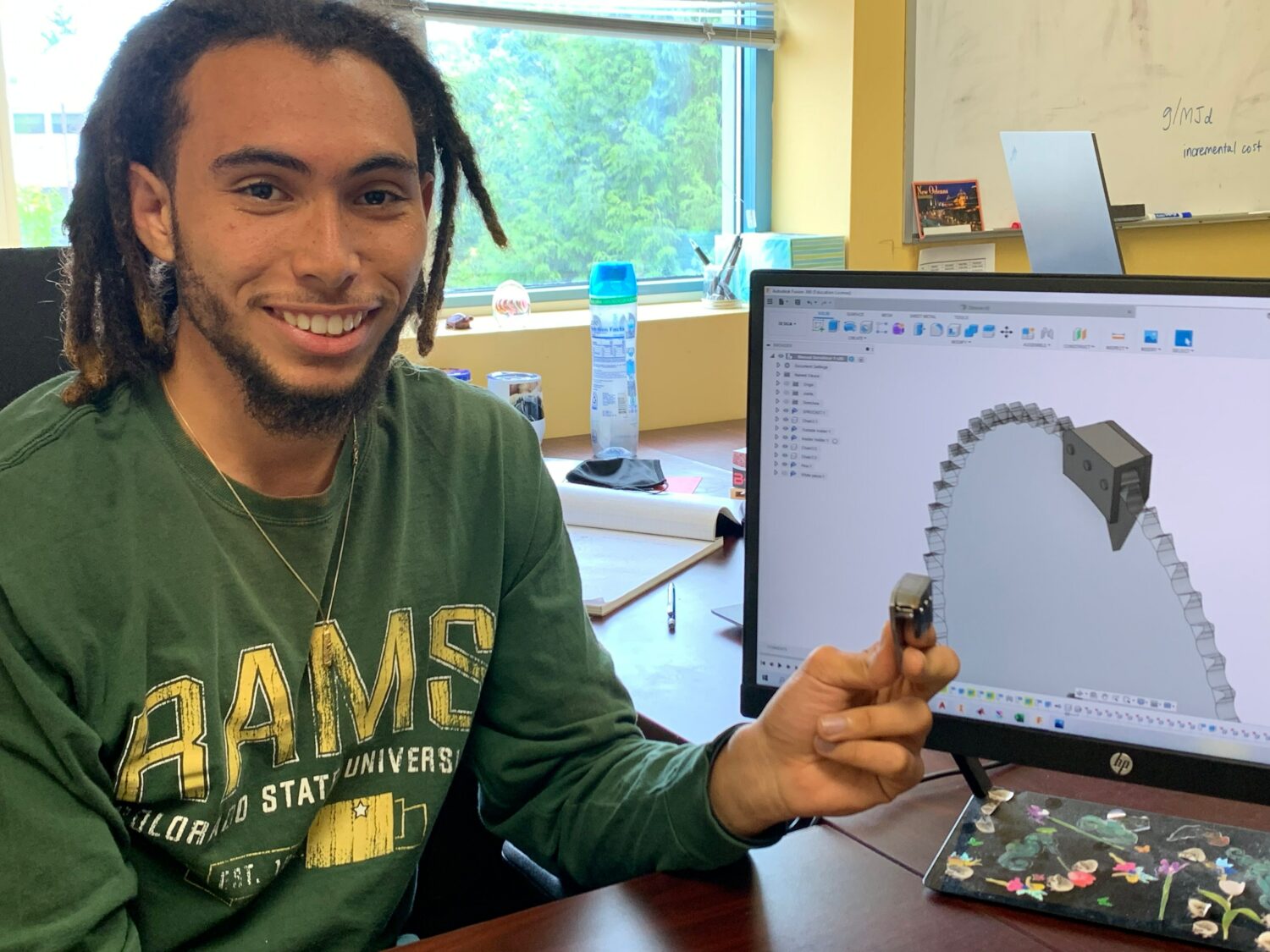
Northeastern University coop student, Thando Ray, designing and prototyping the manual derailleur to load and unload the ergonomic drive mechanism.
The Pilot Phase will consist of working with a selected Ghanaian manufacturer to produce six to ten roasters in-country, which upon completion will be implemented into the field in Northern Ghana. Data will be collected over the course of six or so months to better understand the durability, long-term efficiency, as well as gain more feedback from the women.
To properly implement this technology into Ghana, the team is looking for funding for the project for next year in 2022. As a non-profit organization, BDL relies on grants and donations to continue our work. Please consider supporting us at our donation page.